AixPath is also conducting research and development in publicly funded projects and providing innovative solutions and sophisticated algorithms for several manufacturing technologies. Our area of expertise covers the whole process chain and allows us to develop solutions for CAD, CAM, simulation, integration in third-party software and postprocessing:
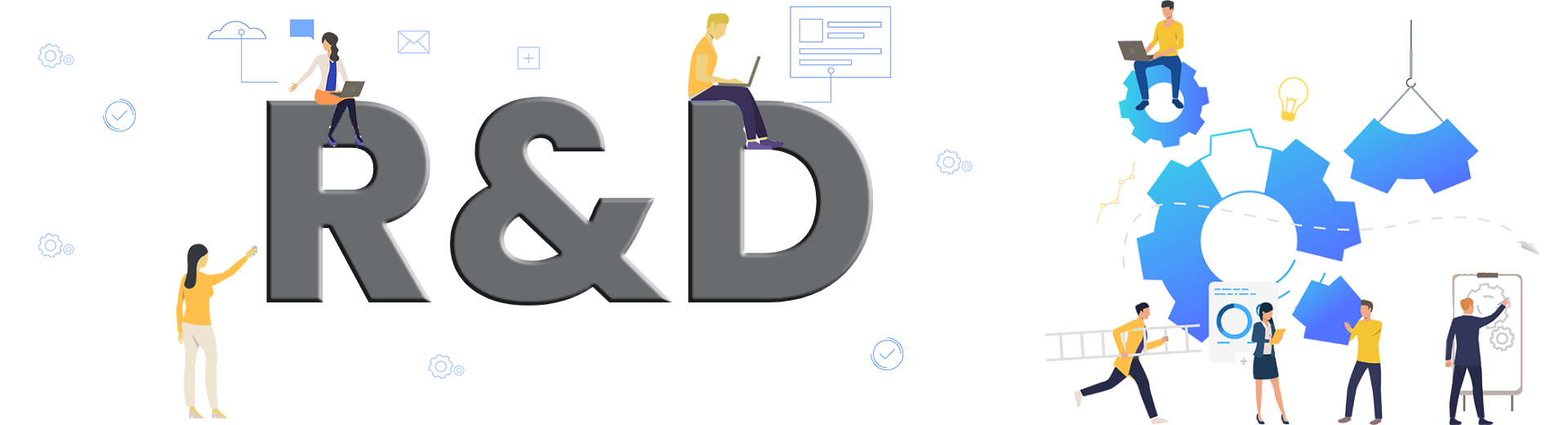
Research and Development
Current Projects
Grindbot is a publicly funded project developing together with ModuleWorks GmbH and Aldakin Automation a Siemens NX PlugIn for robot assisted belt grinding of turbine components. The software prototype enables to fully automate the manual grinding step by a force-controlled automated grinding procedure. Read More
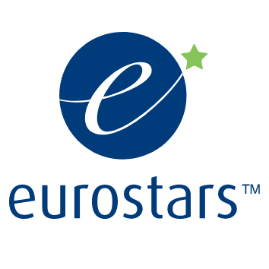
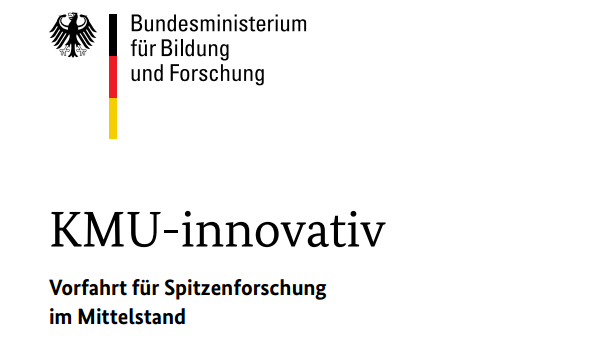
DentalJet is a publicly funded project developing a CAM module for water-jet milling of dental components out of zirconium ceramics. Together with HG Ridder GmbH, who provides the necessary machine technology, the targeted software prototype enables the user to efficiently make use of the water-jet milling technology for dental applications. Read More
Concluded projects
Physix-CAM is a publicly funded project aiming at integrating an in-process-workpiece (IPW) representation of work pieces during the milling process into a PLM system in the sense of a digital twin and combines this with seamless interfaces to FE software. The targeted prototype allows the reduction of dynamic tool and part deflections by up to 70%, reduces tool wear and provides methods to reduce finishing times up to 40% by software optimization. Read More

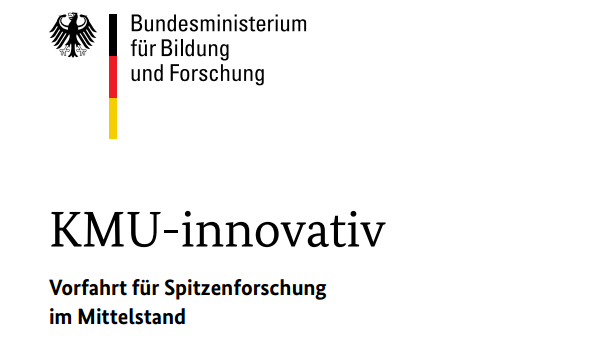
JetCut3D is a publicly funded project developing a CAM module prototype integrated into a PLM system with the capability to precisely predict the deformation of the water-jet during the cutting-process. The targeted software prototype enables the user to efficiently plan and implement water-jet cutting process with a different variety of materials. Read More
MedProd is a publicly funded project focusing on efficient methods of representing complex geometries during the virtual process chain for additive manufacturing. The prototype targets the use of procedurally defined geometries and allows the handling of complex bionic and lattice structures without strain on the computer hardware. Read More
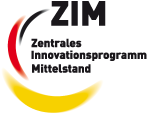
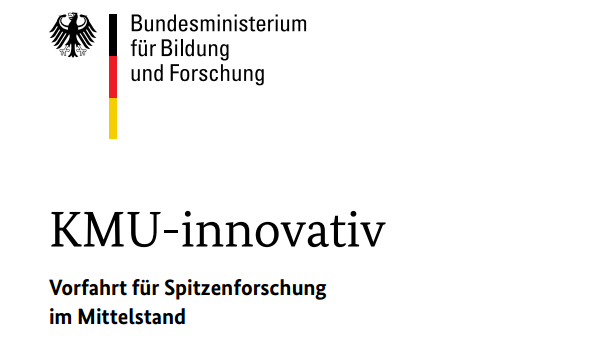
OptiWear was a publicly funded project running from 2017 to 2019. The project goal was to provide a software prototype capable of computing the tool wear during the milling process and optimize based on this date the tool path to reduce local tool wear and increase the longevity of the tool. The developed prototype was integrated into a PLM system. Read More