Medical implants are very critical biomedical technology that must satisfy completely the functionality demands defined by the human body, to avoid any adverse effects. Their manufacturing is therefore a very challenging task that involves utilization of additive manufacturing, subtractive manufacturing, and 3D digitalization technology. The process chain based upon multiple manufacturing technologies are complex and involves intensive use of computer aided technologies for design, manufacturing, and inspection.
Highlights
- Hybrid process: Additive manufacturing for generating part and conventional manufacturing to achieve form accuracy and surface quality
- Using the advantages of each manufacturing technology
- Feature-based machining
Benefits
- Efficient process
- Reduced manufacturing costs and time effort
- High quality parts
- Improved material properties
- High ease-of-use
- Encapsulated knowledge
Funding Call
The “MedProd” project is funded by the Zentrales Innovationsprogramm Mittelstand (ZIM) of the Federal Ministry of Econmic Affairs and Energy (BMWi) (Förderkennzeichen: ZU 4668202HB9)
AiF Projekt GmbH
Tschaikowskistrasse 49
13156 Berlin
E-Mail zim@aif-projekt-gmbh.de

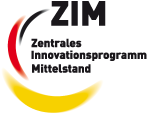
Overview
Current developments in additive manufacturing (AM) have broadened the scope of usable materials and increased material properties of the build-up parts for instance in powder bed fusion processes while the market has due to standardization efforts and higher market demand decreased strongly manufacturing and equipment costs. As a result, the technology 3D printing (additive manufacturing AM) has progressively come in focus by the medical industry. Printers are already producing implant surgical guides, implant restorative setups, orthodontic aligners and retainers, dentures, nightguards and even frameworks (crowns, bridges) plates made of metal (CoCr or titanium). Adding 3D printing technology to the digital workflow moves these efficiencies to the next level, from digital design to the production stage. 3D printing complements traditional processes to streamline production and open the way to new business opportunities. And as its utility and accessibility increase, so does its potential to unlock innovation in unforeseeable ways.
Highlights
- Hybrid process: Additive manufacturing for generating part and conventional manufacturing to achieve form accuracy and surface quality
- Using the advantages of each manufacturing technology
- Feature-based machining
Benefits
- Efficient process
- Reduced manufacturing costs and time effort
- High quality parts
- Improved material properties
- High ease-of-use
- Encapsulated knowledge
Dental implants a very effective in rehabilitation of teeth which are deteriorated due to dental diseases, accidents, or any other reason. Traditionally the manufacturing of dental implants has been carried out by molding and milling technology, which frequent faces quality related issues and the life of such dental implants is reduced. The production process chain established at Premet and utilized by DART is based upon a combined 3D printing and milling process to manufacture dental implants. The process chain allows higher flexibility and control over the manufacturing process. However, the process has potential of improvement in productivity and extended applications for more complex shaped medical implants. In order to utilize the potential in this segment of the market an advanced computer based system for product design, manufacturing planning and process control system is necessary, which could simultaneously handle the complex geometries and utilize the available potential of process technology to the maximum. There is a need for the further development and optimization of the production process of dental bridges and dental / medical plates. Currently the sint&mill process is being implemented and the participating end-customers:
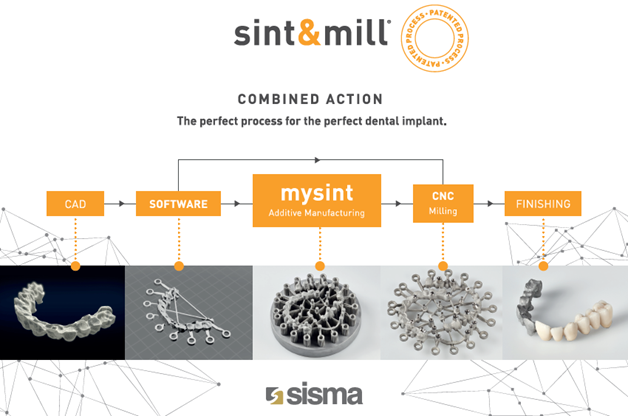
AixPath develops in this project a software tool capable of covering metrology, additive and subtractive manufacturing in one software tool while providing new functionalities to broaden the scope of usable manufacturing strategies, predefined and reusable manufacturing features as well as the necessary functions to refine metrology data automatically and provide a solid basis for the process planning step. This approach broadens the applicability of the solution and provides a software which encapsulates a great portion of the necessary knowledge to implement such process chains in data bases and manufacturing-features and allows the reuse of state-of-the-art solutions for each individual dental prosthesis.
- The targeted software solution provides the following benefits:
- Knowledge encapsulation
- High Ease-of-use
- Feature-based process planning
- Broad scope of applicability in terms of usable standardized abutments
- Usable with different machines and set-ups due to generic post-processor
Project Timeline
Project End - June 2021
Partners
The project is being conducted together with two partners:
Dent-Art-Technik Ltd. is a medical laboratory specialized in manufacturing and trading state-of-the-art medical equipment with a focus on dental technologies for over 25 years. The provide the necessary technology of assembling dental prosthesis, e.g. different state-of-the-art abutments, etc. Furthermore, Dent-Art-Technik has also intensive knowledge and experience with regard to additive manufacturing of dental prosthesis and their material properties.
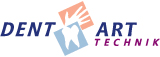
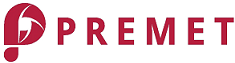
Premet Ltd. is providing the knowledge and the machines to measure and manufacture dental prosthesis by additive and conventional manufacturing. Premet as one of the end customers also provides by selecting appropriate prosthesis and demonstrators the applicability of the developed software in current dental prosthesis manufacturing.